Unleash the power of efficiency! Dive into the world of automated fulfillment processes at Amazon Paterson. Discover how technology speeds up order fulfillment, for a faster delivery experience.
Introduction
Automated fulfillment processes at Amazon Paterson represent a pinnacle of efficiency and innovation in modern logistics. Located in Paterson, this facility harnesses cutting-edge technology to revolutionize the way customer orders are processed, packed, and shipped. By integrating robotics, artificial intelligence, and advanced automation systems, Amazon has streamlined operations to meet the growing demands of e-commerce. This introduction explores how these automated processes optimize efficiency, improve accuracy, and enhance overall customer satisfaction, setting a new standard in the realm of fulfillment centers.
Automated fulfillment processes at Amazon Paterson
The Amazon fulfillment center in Paterson, New Jersey, epitomizes the future of e-commerce logistics through its extensive use of automation and advanced technology. As one of the most sophisticated facilities in Amazon’s global network, it showcases a seamless integration of robotics, software, and human ingenuity to achieve unparalleled efficiency and accuracy in order fulfillment.
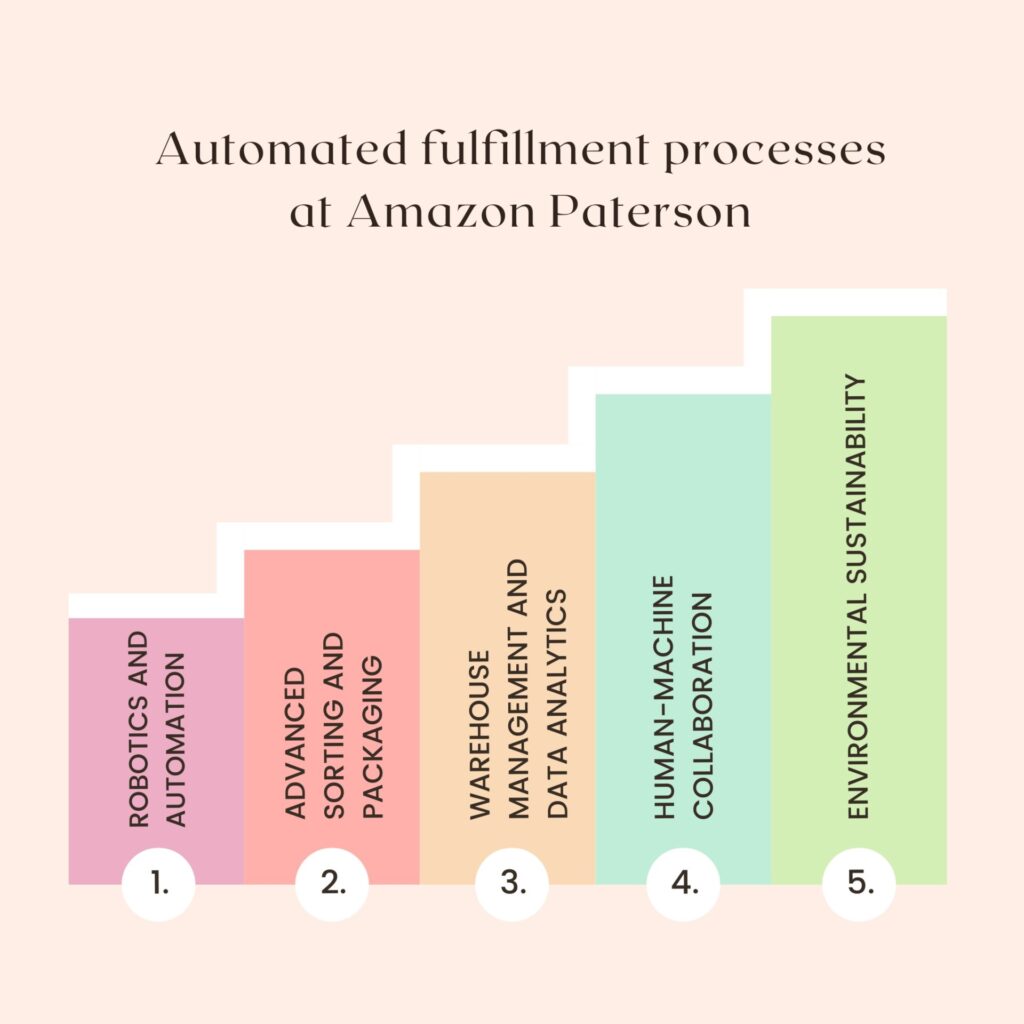
Robotics and Automation
- Kiva Robots Central to Amazon Paterson’s automation are the Kiva robots. These autonomous mobile robots (AMRs) glide across the warehouse floor, carrying entire shelves of products to human workers at picking stations. This minimizes the time workers spend walking around the warehouse, allowing them to focus on tasks that require human dexterity and judgment. Each robot can carry up to 1,000 pounds and is guided by a grid of QR codes on the floor, ensuring precise navigation and coordination.
- Automated Storage and Retrieval Systems (AS/RS) The facility employs sophisticated AS/RS to manage inventory. These systems use cranes and shuttles to store and retrieve items from high-density storage racks, optimizing space utilization and speeding up the process of locating products. The integration of AS/RS with Amazon’s Warehouse Management System (WMS) allows for real-time inventory tracking and seamless order processing.
- Vision Systems and Machine Learning Vision systems powered by machine learning algorithms are used extensively for quality control and inventory management. High-resolution cameras and sensors capture detailed images of products and packaging, which are analyzed to detect defects, ensure correct labeling, and verify that the right items are picked. This reduces errors and enhances the overall quality of service.
Advanced Sorting and Packaging
- Automated Sortation Centers After items are picked, they are transported to automated sortation centers where advanced conveyor systems and sortation machines categorize packages by destination. These systems use barcode scanners and optical character recognition (OCR) technology to read labels and sort packages at remarkable speeds, ensuring that each order is directed to the appropriate shipping lane.
- Custom Packaging Solutions Amazon Paterson features automated packaging machines that customize boxes to the exact dimensions of the products. This not only reduces packaging waste but also ensures that items are securely packed, minimizing damage during transit. The machines automatically measure, cut, fold, and seal the packages, and print shipping labels, readying them for dispatch with minimal human intervention.
- Robotic Palletizing At the end of the sortation and packaging line, robotic arms are employed for palletizing—stacking boxes onto pallets for shipment. These robots can handle heavy loads and arrange packages efficiently, maximizing space on trucks and reducing shipping costs.
Warehouse Management and Data Analytics
- Real-Time Data Integration The Warehouse Management System (WMS) at Amazon Paterson integrates data from various sources, including robotics, inventory systems, and shipping databases, to provide a comprehensive view of warehouse operations. This real-time data integration enables dynamic decision-making, such as rerouting items to different packing stations based on workload and order priority.
- Predictive Analytics and AI Predictive analytics and artificial intelligence (AI) play a critical role in forecasting demand, managing inventory levels, and optimizing labor deployment. Machine learning models analyze historical data and current trends to predict which products will be in high demand, allowing Amazon to preemptively stock and position items strategically within the warehouse. This reduces stockouts and ensures faster fulfillment.
- Performance Monitoring and Continuous Improvement Performance metrics and key performance indicators (KPIs) are continuously monitored to identify bottlenecks and areas for improvement. The WMS generates detailed reports on various aspects of warehouse operations, from pick rates to error rates, enabling Amazon to implement continuous improvement strategies and maintain high efficiency.
Human-Machine Collaboration
- Enhanced Worker Safety and Productivity The automation at Amazon Paterson enhances worker safety by reducing the need for manual lifting and repetitive tasks. Workers are trained to operate and collaborate with advanced machinery, focusing on tasks that require human intelligence and adaptability. This collaborative approach not only improves safety but also boosts productivity and job satisfaction.
- Skilled Workforce Development Amazon invests in training programs to equip its workforce with the skills needed to operate and maintain advanced robotic systems. Employees receive continuous education on the latest technologies and best practices, fostering a culture of innovation and adaptability.
Environmental Sustainability
- Energy-Efficient Operations The automation systems at Amazon Paterson are designed with energy efficiency in mind. Robotics and AS/RS systems consume less power compared to traditional warehouse operations, contributing to Amazon’s sustainability goals. Additionally, the facility utilizes energy-efficient lighting and climate control systems to reduce its carbon footprint.
- Waste Reduction Initiatives Automated packaging systems help minimize waste by creating custom-sized boxes that use less material. Furthermore, Amazon has implemented recycling programs and waste management strategies to ensure that packaging materials are reused or disposed of in an environmentally friendly manner.
The Future of Automated Fulfillment
Amazon’s investment in automation at its Paterson facility represents a significant step toward the future of e-commerce logistics. As technology continues to evolve, we can expect even greater levels of efficiency, accuracy, and sustainability in order fulfillment. Innovations such as drone delivery, autonomous vehicles, and advanced AI algorithms will further transform the landscape, making the supply chain more resilient and responsive to customer needs.
Benefits of Automated Fulfillment Processes at Amazon Paterson
Amazon’s fulfillment centers are known for their efficiency and innovation, and the facility in Paterson is no exception. By incorporating advanced automation technologies, Amazon Paterson has streamlined its operations, offering several key benefits.
1. Increased Efficiency
Automation significantly boosts the speed and accuracy of the fulfillment process. With robots handling repetitive tasks, items can be picked, packed, and shipped much faster than manual labor. This efficiency not only reduces the time it takes for customers to receive their orders but also allows Amazon Paterson to process a higher volume of orders daily.
2. Improved Accuracy
Automated systems minimize human error, ensuring that the correct items are picked and packed. This leads to higher customer satisfaction, as orders are more likely to be accurate and arrive in good condition. Barcoding and scanning technologies further enhance accuracy by verifying items at multiple stages.
3. Cost Savings
By reducing the need for manual labor, automation helps cut operational costs. Although the initial investment in automation technology can be high, the long-term savings in labor costs and increased throughput can make it a cost-effective solution. Additionally, automation can reduce the need for seasonal hiring during peak times, further lowering expenses.
4. Enhanced Safety
Automation improves workplace safety by taking over dangerous or physically demanding tasks. Robots can handle heavy lifting, repetitive movements, and hazardous environments, reducing the risk of injuries among human workers. This leads to a safer working environment and can decrease the number of worker compensation claims.
5. Scalability
Automated systems are highly scalable, allowing Amazon Paterson to adjust its operations quickly in response to demand fluctuations. During peak shopping periods, such as holidays or special sales events, the facility can ramp up its processing capabilities without the need for significant manual labor adjustments.
6. Better Inventory Management
Automated systems provide real-time data on inventory levels, improving stock management and reducing the likelihood of stockouts or overstock situations. This real-time visibility helps in making informed decisions about inventory replenishment and product allocation, ensuring that popular items are always available for customers.
7. Environmental Impact
Automation can contribute to more sustainable operations. Efficient processes reduce energy consumption and waste. Moreover, automated systems can optimize packaging processes, using the right amount of materials, which reduces waste and supports Amazon’s broader sustainability goals.
8. Consistency and Reliability
Automated systems operate consistently around the clock, without the need for breaks or shifts. This reliability ensures a continuous flow of operations, which is essential for meeting customer expectations for fast and reliable delivery.
Challenges in Implementing Automation at Amazon Paterson
While the benefits of automation at Amazon’s Paterson fulfillment center are significant, the path to implementing these advanced technologies is not without its challenges. Below are some of the primary obstacles faced during the automation process.
1. High Initial Costs
Implementing automation involves substantial upfront investments in robotics, software, and infrastructure. The cost of purchasing, installing, and maintaining automated systems can be a major financial burden. For Amazon Paterson, balancing these costs with the expected long-term savings is a critical challenge.
2. Technical Integration
Integrating new automated systems with existing operations and technology can be complex. Ensuring compatibility between different technologies and maintaining seamless communication across systems requires sophisticated IT solutions and expertise. Any integration issues can disrupt operations and lead to inefficiencies.
3. Workforce Adaptation
The transition to automated systems necessitates significant changes in the workforce. Employees must adapt to new roles that involve managing and maintaining automation technologies. This shift can be challenging, requiring comprehensive training programs and sometimes leading to resistance from employees who may be apprehensive about the changes.
4. Downtime and Maintenance
Automation systems require regular maintenance to ensure they operate efficiently. Any downtime for repairs or upgrades can disrupt the fulfillment process, leading to potential delays in order processing. Developing a robust maintenance schedule and having contingency plans in place are essential to minimize disruptions.
5. Data Security and Privacy
Automated systems rely heavily on data collection and processing, raising concerns about data security and privacy. Protecting sensitive information from cyber threats and ensuring compliance with data protection regulations is a significant challenge. Robust cybersecurity measures must be implemented to safeguard data integrity.
6. Scalability Issues
While automation is designed to enhance scalability, initial implementation can present scalability challenges. Ensuring that automated systems can handle both current and future volumes requires careful planning and flexible design. Overcoming these challenges is crucial to maintain efficiency as demand fluctuates.
7. Complex Decision-Making
Automation often involves complex decision-making algorithms and artificial intelligence. Developing and fine-tuning these algorithms to handle the nuances of fulfillment operations is a major challenge. Ensuring that automated systems can make accurate and effective decisions in various scenarios requires ongoing monitoring and adjustments.
8. Regulatory Compliance
Adhering to regulatory standards and industry guidelines is critical when implementing automation. Amazon Paterson must navigate a complex landscape of regulations related to labor, safety, and data protection. Ensuring compliance while implementing cutting-edge technologies can be a difficult balancing act.
9. Physical Space Limitations
Retrofitting existing facilities to accommodate automation technologies can be challenging due to space constraints. Designing layouts that maximize efficiency while fitting within the physical limitations of the building requires careful planning and potentially significant modifications.
10. Vendor Dependence
Reliance on external vendors for automation technologies can present risks. Dependence on vendors for support, updates, and repairs means that any issues with the vendor can directly impact the facility’s operations. Developing strong vendor relationships and having contingency plans is essential to mitigate this risk.
A Day in the Life of an Amazon Paterson Fulfillment Center
The Amazon Paterson fulfillment center is a bustling hub of activity, where technology and human effort come together to ensure that customers receive their orders quickly and efficiently. Here’s a glimpse into a typical day at this state-of-the-art facility.
Early Morning: Preparation and Planning
The day begins early at Amazon Paterson. As the first shift arrives, the facility is already buzzing with energy. Managers and team leaders hold briefings to outline the day’s goals, assign tasks, and address any issues from the previous day. Employees don their safety gear and head to their respective stations, ready to tackle the day’s workload.
Morning Shift: Receiving and Stowing
As the sun rises, delivery trucks begin arriving at the loading docks. The receiving team is responsible for unloading these trucks, scanning incoming products, and checking them against the inventory list. Items are then sorted and placed on conveyor belts that transport them to various parts of the warehouse.
Stowers take over from here, placing items in designated storage locations. Using handheld scanners, they ensure that each product is correctly logged in the inventory system. This precise organization allows for quick and accurate retrieval later in the day.
Mid-Morning: Picking and Packing
By mid-morning, the picking process is in full swing. When a customer places an order, a signal is sent to the pickers, who locate the items in the warehouse. Guided by a combination of advanced software and handheld devices, pickers navigate the vast aisles efficiently.
Once the items are picked, they are sent to the packing area. Here, packers ensure that each item is securely packed, labeled, and ready for shipping. Automation plays a key role, with machines assisting in the packaging process to enhance speed and accuracy.
Lunchtime: Brief Pause and Shift Change
Around noon, the first shift begins to wind down, and the lunchtime period provides a brief respite for the hardworking staff. The break room fills with employees taking a well-deserved rest, sharing stories, and recharging for the second half of their shift. Meanwhile, the second shift starts to arrive, ready to continue the momentum.
Afternoon: Quality Control and Shipping
In the afternoon, quality control takes center stage. Quality assurance teams conduct random checks to ensure that orders are accurate and items are in perfect condition. Any discrepancies are quickly addressed to maintain high standards.
Simultaneously, the shipping department is in high gear. Packed orders are sorted based on their destinations and loaded onto trucks. These trucks, destined for various locations, ensure that customers receive their purchases as quickly as possible.
Late Afternoon: Continuous Improvement
As the day progresses, the focus shifts towards continuous improvement. Team leaders and managers analyze performance data, identifying areas for improvement. Feedback from employees is encouraged, fostering a culture of collaboration and innovation. Any issues encountered during the day are addressed in real-time to prevent future occurrences.
Evening: Wrapping Up and Transition
As the evening approaches, the third shift arrives to take over operations. The handover between shifts is seamless, with detailed reports and briefings ensuring that everyone is on the same page. The focus remains on maintaining efficiency and meeting daily targets.
Night Shift: Maintenance and Preparation for the Next Day
During the night shift, the facility undergoes maintenance. Technicians perform routine checks on machinery and automated systems, ensuring that everything is in optimal condition for the next day. The night crew also prepares the warehouse for the incoming day’s activities, restocking supplies, and organizing workstations.
FAQ’s
What are the main challenges of implementing automated fulfillment processes at Amazon Paterson?
Challenges may include the initial investment in technology, integration of complex systems, training staff to work alongside automation, and ensuring seamless coordination between different automated processes.
How does Amazon Paterson ensure the accuracy of orders with automation?
Automation systems at Amazon Paterson are designed with built-in quality checks, barcode scanning, and real-time data analytics to ensure accuracy in picking, packing, and shipping orders.
Can customers track their orders processed through automated fulfillment at Amazon Paterson?
Yes, customers can track their orders in real-time through Amazon’s tracking system, which provides updates on order status, estimated delivery times, and package location.
What are the environmental benefits of automated fulfillment processes at Amazon Paterson?
Automation helps to optimize warehouse space, reduce energy consumption, and minimize packaging waste, contributing to Amazon’s sustainability goals.
How does Amazon Paterson plan to further innovate its automated fulfillment processes in the future?
Amazon continually invests in research and development to enhance automation technologies, exploring advancements in robotics, artificial intelligence, and predictive analytics to further optimize fulfillment operations.
Conclusion
The automated fulfillment processes at Amazon Paterson exemplify a transformative approach to modern logistics and e-commerce operations. By leveraging advanced technologies such as robotics, machine learning, and automated systems, Amazon has significantly enhanced efficiency, accuracy, and speed in order fulfillment. These innovations not only streamline the processing of customer orders but also contribute to faster delivery times and improved customer satisfaction. While automation plays a central role, human oversight remains crucial for quality control and maintenance of these sophisticated systems. Looking ahead, Amazon Paterson’s commitment to continuous innovation promises further enhancements in automation, aiming to redefine the standards of efficiency and reliability in fulfillment services.