Unleash the power of innovation! Explore Advanced warehouse automation by Amazon in Paterson. Discover how robotics and automation are revolutionizing fulfillment, boosting efficiency, and speeding up deliveries.
Introduction
Advanced warehouse automation is revolutionizing the way businesses operate, and Amazon is at the forefront of this transformation in Paterson. With the integration of cutting-edge technology and innovative practices, Amazon has set a new standard for efficiency and productivity in warehouse management. This automation not only streamlines operations but also significantly reduces costs and improves accuracy. In Paterson, Amazon’s advanced warehouse automation includes the use of robotics, artificial intelligence, and sophisticated software systems that work together to enhance the entire supply chain process. This introduction will explore the various aspects of Amazon’s warehouse automation in Paterson, highlighting its impact on the industry and the local economy.
Advanced warehouse automation by Amazon in Paterson
Advanced Warehouse Automation
Warehouse automation represents a significant shift in the logistics and supply chain industry, driven by the need to increase efficiency, reduce costs, and improve accuracy in operations. Advanced warehouse automation leverages cutting-edge technologies such as robotics, artificial intelligence (AI), and the Internet of Things (IoT) to streamline processes and enhance productivity. This article explores the key aspects and benefits of advanced warehouse automation.
Key Technologies in Advanced Warehouse Automation
- Robotics: Automated robots are increasingly used in warehouses to perform repetitive tasks such as picking, packing, sorting, and transporting goods. These robots can operate around the clock, optimizing workflows and reducing the need for human labor in high-risk or highly repetitive tasks.
- Artificial Intelligence (AI): AI plays a crucial role in warehouse automation by enabling smart decision-making and improving operational efficiencies. AI algorithms can predict inventory trends, optimize stock levels, and manage supply chain logistics dynamically.
- Internet of Things (IoT): IoT devices collect and transmit data in real-time, allowing for continuous monitoring of warehouse operations. This connectivity not only helps in tracking inventory but also enhances the accuracy of order fulfillment processes.
- Automated Storage and Retrieval Systems (ASRS): ASRS are critical in optimizing storage spaces and improving retrieval times. These systems can adjust dynamically to inventory sizes and weights, maximizing space utilization and reducing waste.
- Drones: Drones are used for inventory checks and monitoring within large warehouse spaces. They provide a bird’s eye view of operations, helping in quick identification of issues and ensuring consistent stock levels.
Benefits of Advanced Warehouse Automation
- Increased Efficiency: Automation significantly speeds up various warehouse operations, from inventory management to order processing, leading to faster turnaround times.
- Cost Reduction: By reducing reliance on manual labor and enhancing operational efficiency, companies can significantly lower operational costs.
- Accuracy and Reliability: Automated systems minimize human errors in inventory management and order processing, ensuring higher reliability and customer satisfaction.
- Scalability: Automated systems can be scaled up or down based on business needs without the proportional increase in workforce, providing flexibility in operations.
- Safety: With robots handling hazardous tasks, the workplace becomes safer for human employees, reducing the risk of accidents.
Implementation Challenges
While the benefits are substantial, implementing advanced warehouse automation can pose challenges, including high initial investment costs, the complexity of integration with existing systems, and the need for skilled personnel to manage and maintain automated systems.
The Future of Warehouse Automation
As technology continues to advance, the scope of warehouse automation will expand, incorporating more sophisticated AI algorithms, advanced robotics, and more comprehensive IoT networks. The future warehouse is envisioned as a fully automated facility with minimal human intervention, characterized by high efficiency and precision.
Warehouse automation is not just a trend but a necessary evolution in the face of growing global demand and the ever-increasing pace of commerce. Companies embracing this technology will likely lead in efficiency, cost management, and customer satisfaction, setting new standards in the logistics industry.
Amazon’s Advanced Automation Technologies
Amazon, a global leader in e-commerce, continuously seeks to enhance operational efficiency and customer satisfaction through cutting-edge automation technologies. By integrating sophisticated robotics, artificial intelligence (AI), and other advanced technologies, Amazon sets the standard for innovation in warehouse management and logistics. This article explores the key automation technologies utilized by Amazon and their impact on the industry.
Core Components of Amazon’s Automation Strategy
- Kiva Robots: One of the early adopters of robotics in warehouse operations, Amazon utilizes Kiva robots to move entire shelves of products to human packers. This not only speeds up the processing time but also reduces physical strain on workers, significantly boosting productivity and space efficiency.
- Amazon Robotics Sortable (ARS): ARS is designed to automate the picking and packing process, using robotics to handle individual items. This system is crucial in managing the vast variety of products in Amazon’s inventory, ensuring accurate and timely deliveries.
- Drones – Prime Air: Amazon is at the forefront of using drones for delivery with its Prime Air service. These drones are designed to safely get packages to customers in 30 minutes or less, dramatically reducing delivery times and costs associated with traditional methods.
- Artificial Intelligence and Machine Learning: AI and machine learning algorithms are integral to Amazon’s operations, used for predicting shopping trends, managing inventory, optimizing logistics, and personalizing customer experiences. This technology allows Amazon to anticipate customer needs and adjust its strategies in real-time.
- Automated Packaging Machines: Amazon employs automated packaging machines that can scan and package orders much faster than manual processes. These machines significantly reduce packaging material waste and improve the efficiency of the packing process.
Benefits of Amazon’s Automation Technologies
- Enhanced Efficiency: Automation enables Amazon to handle millions of orders with extraordinary speed and accuracy, maintaining its reputation for quick delivery times.
- Scalability: Automation supports Amazon’s scalability, allowing for rapid expansion into new markets without a proportionate increase in labor costs.
- Reduced Operational Costs: By automating various processes, Amazon can operate more leanly, saving on labor costs and reducing human error.
- Improved Customer Satisfaction: Faster processing and delivery times, along with fewer errors, lead to higher customer satisfaction and loyalty.
Challenges and Considerations
Implementing such advanced automation is not without challenges. These include high initial investments, the technical complexity of integrating various systems, and the socio-economic impacts of reducing the human workforce. Amazon continues to address these challenges by investing in employee retraining programs and continuously improving their technologies.
The Future Direction
Amazon is likely to continue its investment in automation technologies, exploring new avenues such as robotic innovation, enhanced AI capabilities, and more efficient delivery methods. The ongoing development of Amazon’s technological infrastructure aims not only to improve internal operations but also to set a benchmark for the entire logistics and retail industry.
Amazon’s commitment to advanced automation technologies is a testament to the company’s forward-thinking approach, ensuring it remains at the cutting edge of the e-commerce industry while redefining the possibilities of logistics and supply chain management.
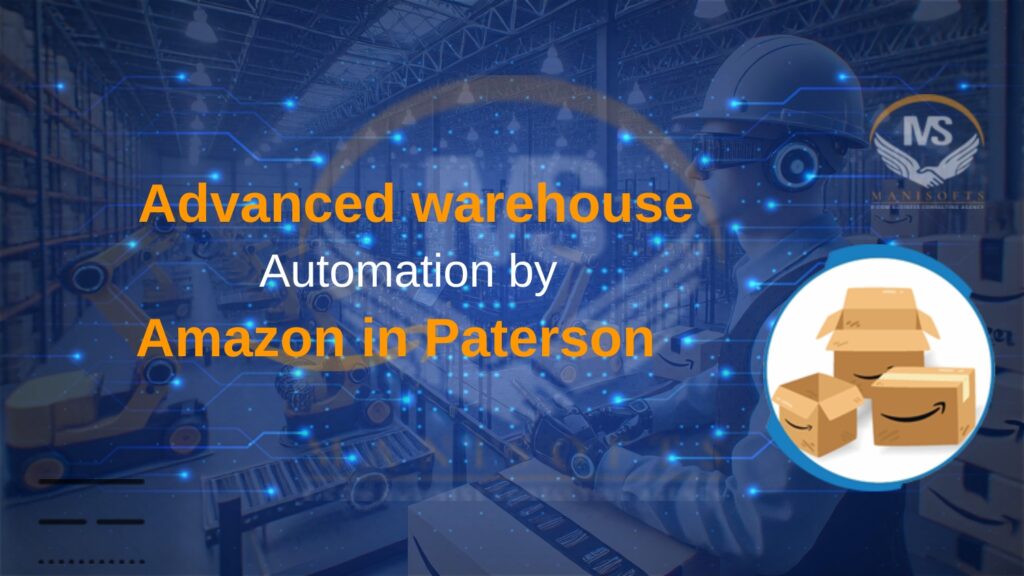
Implementation of Automation in Paterson
Paterson, New Jersey, has emerged as a significant hub for technological advancements, particularly in the implementation of automation across various industries. The city’s strategic selection for automation projects is driven by several key factors, and the rollout of these initiatives follows a carefully structured timeline and multiple stages.
Reasons for Choosing Paterson for Automation
- Strategic Location: Paterson’s proximity to major metropolitan areas like New York City makes it an ideal location for companies looking to optimize logistics and distribution. Its location allows for quick access to one of the largest consumer markets in the United States, making it highly attractive for automated warehousing and manufacturing facilities.
- Industrial History: Paterson has a rich industrial history, once known as the “Silk City” for its dominant role in silk production in the 19th century. This historical significance continues today as the city transforms into a modern industrial hub, leveraging its experienced workforce and industrial spaces that are ideal for retrofitting with new technologies.
- Economic Revitalization Efforts: The city has been the focus of numerous economic revitalization efforts, which include attracting technology-driven companies. These efforts make Paterson an appealing choice for businesses looking to implement automation, as they can benefit from local incentives and support from city and state governments.
- Access to Talent: With several universities and technical schools in and around Paterson, there is a steady stream of skilled graduates ready to work in technologically advanced environments. This educational infrastructure supports ongoing training and development in automation technologies.
Timeline and Stages of Implementation
Stage 1: Planning and Feasibility (2020-2021)
The initial stage involved comprehensive planning and feasibility studies. Key activities included assessing local infrastructure, engaging with community leaders and stakeholders, and identifying potential sites for automation projects. This phase also involved detailed cost-benefit analyses to ensure the sustainability of the investment in automation technologies.
Stage 2: Infrastructure Development (2021-2022)
Following the planning phase, the focus shifted to developing the necessary infrastructure. This included upgrading utilities, enhancing broadband connectivity, and retrofitting old industrial buildings to accommodate new technologies. Significant investments were made in creating a supportive environment for automation systems.
Stage 3: Pilot Testing (2022-2023)
Pilot projects were launched in selected facilities to test the efficiency and effectiveness of automation systems under real-world conditions. These pilot tests helped identify any potential issues and allowed for adjustments before a full-scale rollout. Key industries involved in this stage included manufacturing, logistics, and retail.
Stage 4: Full-scale Implementation (2023-Present)
With successful pilot testing, Paterson moved to full-scale implementation. This current stage sees widespread adoption of automation technologies across various sectors. Continuous monitoring and optimization processes are in place to ensure that the systems deliver the intended benefits such as increased productivity, cost savings, and improved safety.
Challenges and Solutions in Automation
Implementing automation, while beneficial, comes with its own set of challenges. Amazon, a leader in warehouse automation and technological innovation, has faced various hurdles in this journey. Their experiences provide valuable lessons in overcoming these challenges through strategic planning and innovative solutions.
Common Challenges Faced During Automation
- Integration with Existing Systems: One of the significant challenges is integrating new automation technologies with existing systems without disrupting ongoing operations. This can be complex when older systems are not compatible with new technologies.
- Workforce Adaptation: The introduction of automation can lead to uncertainty and resistance among employees. Workers may fear job displacement or struggle to adapt to new roles that require different skills.
- High Initial Costs: The upfront cost of implementing automated systems can be prohibitively high. This includes not just the cost of the technology itself but also training, installation, and potential downtime during the transition.
- Maintenance and Technical Issues: Automated systems require high maintenance and can face technical glitches. The complexity of these systems means that any malfunction can lead to significant downtime and disrupt the entire operation.
- Data Security and Privacy: As automation often relies heavily on data, ensuring the security and privacy of this data becomes a critical challenge, especially in industries dealing with sensitive information.
Strategies Used by Amazon to Overcome These Challenges
- Phased Integration: Amazon approaches the integration of automation technologies in a phased manner. This allows the company to test new systems on a small scale before fully integrating them across operations. This step-by-step approach helps mitigate the risk of significant disruptions and allows time for troubleshooting and optimization.
- Employee Re-skilling and Support: To address workforce concerns, Amazon invests in extensive training and development programs. They provide their employees with the skills needed to work alongside automated systems, thus transitioning them into more technical roles and reducing resistance to change.
- Cost-Benefit Analysis and Scalable Investments: Amazon conducts thorough cost-benefit analyses to justify the high initial costs of automation. They also scale their investments based on the performance of automation in pilot projects, ensuring that resources are allocated efficiently and can yield measurable benefits.
- Regular Maintenance and Technical Support: Amazon maintains a dedicated team for the maintenance and technical support of automated systems. This team works round the clock to quickly address any issues, minimizing downtime and ensuring the smooth operation of their automated facilities.
- Robust Cybersecurity Measures: To protect data integrity and privacy, Amazon implements stringent cybersecurity measures. These include data encryption, secure access protocols, and regular audits to prevent breaches and ensure compliance with global data protection regulations.
FAQ’s
Enhanced Efficiency: Warehouse automation surpasses manual operations in both speed and precision, leading to marked improvements in the time it takes to fulfill orders and the accuracy of those orders. Reduced Labor Costs: Automation reduces the number of workers needed to manage warehouse operations, leading to significant savings in labor expenses.
Automation significantly reduces the time from order to shipment at the Paterson warehouse, enabling faster delivery times and more responsive customer service.
Yes, AI is employed at Amazon’s Paterson facility to accurately predict inventory demands, optimize stock levels, and prevent overstocking or stockouts, ensuring efficient inventory management.
Amazon occasionally offers tours of its facilities, including the Paterson warehouse, allowing the public to see the automation technology in action. Interested individuals should check Amazon’s official website for tour availability.
Amazon ensures the reliability of its automated systems in Paterson through regular maintenance, continuous monitoring, and updates to both hardware and software components as needed.
Conclusion
Amazon’s implementation of advanced warehouse automation in Paterson represents a significant leap forward in the realm of logistics and supply chain management. By integrating state-of-the-art robotics, artificial intelligence, and automated systems, Amazon has not only enhanced the efficiency and accuracy of its warehouse operations but also set a new standard for the industry. This technological advancement ensures quicker order fulfillment, reduced labor costs, and improved safety conditions, ultimately benefiting both the company and its customers. As Amazon continues to refine and expand its automation technologies, the Paterson facility stands as a testament to the potential of modern automation to transform traditional warehouse practices into dynamic, highly efficient systems.